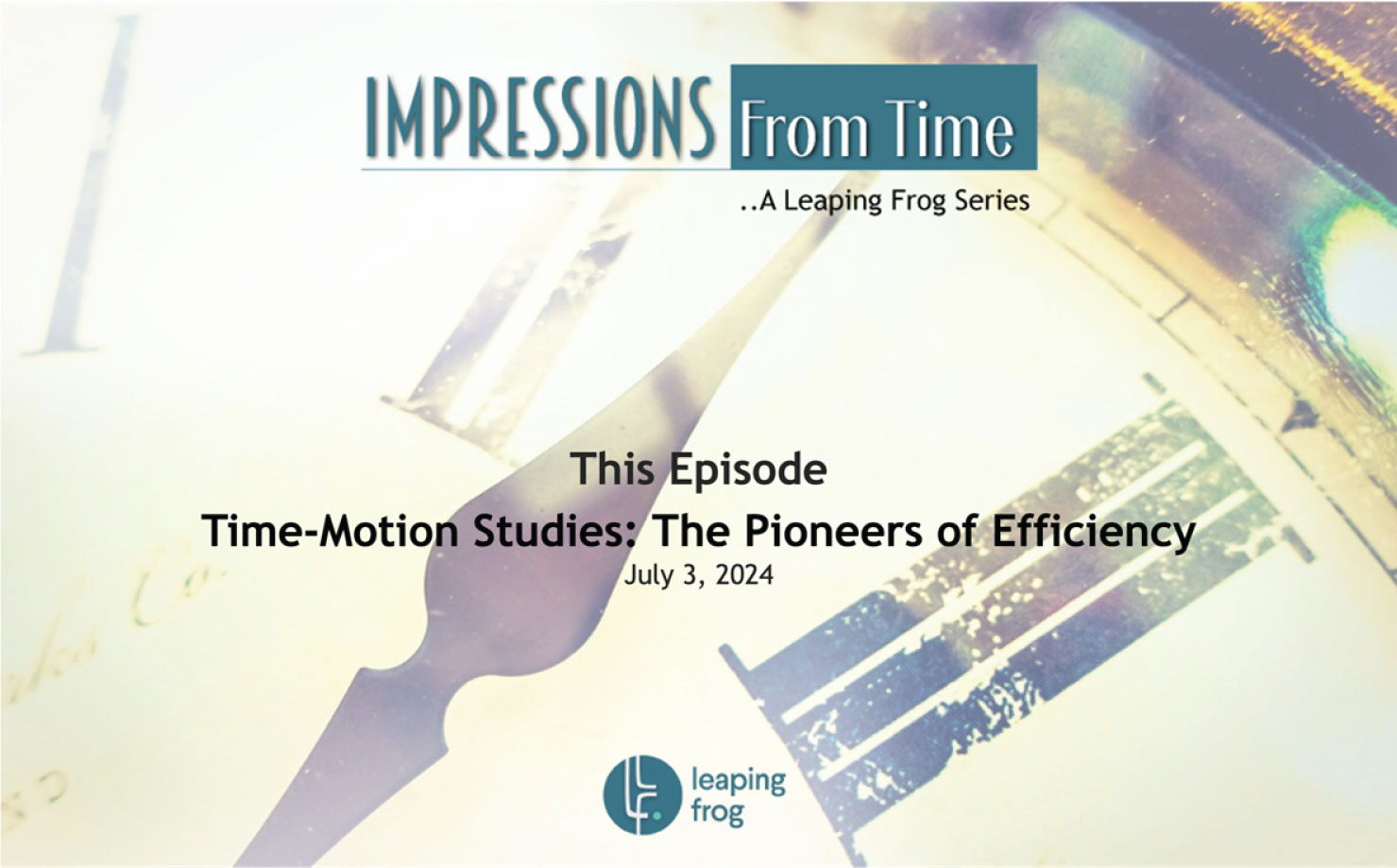
Few industrial engineering and management contributions are as seminal as the time-motion studies pioneered by Frederick Taylor and the husband-and-wife team of Frank and Lillian Gilbreth in the early 20th century. These studies laid the foundation for modern efficiency and productivity optimisation practices.
Frederick Winslow Taylor, often dubbed the “father of scientific management,” introduced principles that transformed the industrial workplace. Born in 1856, Taylor began his career as a mechanical engineer and quickly grew disillusioned with the inefficiencies he observed in manufacturing processes. His solution was a systematic study of work to find the “one best way” to perform each task.
The Story Behind the Research
Taylor’s groundbreaking work involved detailed time studies where he meticulously observed and timed each task performed by workers.
Taylor’s initial research was conducted at the Bethlehem Steel Company in Pennsylvania. With his background in mechanical engineering, Taylor was deeply interested in improving industrial efficiency. He observed that workers at Bethlehem Steel performed tasks in various ways, often inefficiently. This inconsistency intrigued him, prompting the question: Could work processes be standardised to enhance productivity?
To answer this, Taylor introduced a method known as time and motion studies. He selected a group of workers, with Schmidt, a Dutch immigrant labourer, as his primary subject. Schmidt was chosen because he embodied the average worker at the plant, and Taylor believed that if he could improve Schmidt’s performance, he could improve anyone’s.
The process began with Taylor and his assistants meticulously observing and recording every action Schmidt performed during his workday. They used stopwatches to measure the time taken for each task and recorded these observations in detailed logs. They also analysed Schmidt’s movements, noting which were necessary and which were superfluous.
For instance, Schmidt was responsible for loading pig iron onto rail cars. Taylor and his team broke down this seemingly simple task into its constituent motions: bending to pick up the pig iron, lifting it, turning, walking to the rail car, and placing it onto the vehicle. Each of these actions was timed and analysed.
Taylor found that Schmidt often took unnecessary steps and movements that could have been more productive. To combat this, Taylor devised a series of optimised procedures, eliminating unnecessary motions and teaching Schmidt the most efficient way to perform each task. He even determined the ideal weight of pig iron Schmidt should carry to maximise his productivity without exhausting him.
With these new methods in place, Schmidt’s productivity soared. He went from loading 12.5 tons of pig iron daily to 47 tons, a nearly fourfold increase. Taylor’s meticulous records and analysis demonstrated that standardising work processes and reducing unnecessary movements could dramatically improve efficiency.
The success of these time and motion studies didn’t just benefit the Bethlehem Steel Company. They laid the foundation for modern industrial engineering and management practices. Taylor’s work emphasised the importance of scientific analysis in the workplace, advocating for carefully studying tasks to optimise worker productivity.
Frank and Lillian Gilbreth: Motion Study Innovators
While Taylor focused on time study, Frank and Lillian Gilbreth expanded the field by developing motion study. Originally a bricklayer, Frank Gilbreth observed that workers often performed unnecessary movements that reduced efficiency. His insight led him to devise methods for streamlining tasks, starting with bricklaying.
The Gilbreths used motion picture technology, a novel approach at the time, to film workers performing various tasks. This allowed them to analyse the footage frame by frame, identify unnecessary motions, and devise more efficient ways to perform tasks. They broke down tasks into smaller, more manageable components and developed “therbligs,” a set of 18 elemental motions that could be analysed and optimised.
One of their significant studies involved the surgical field, where they worked with Dr. Richard C. Cabot at Harvard Medical School. They filmed surgical procedures and analysed the movements of surgeons and nurses to eliminate wasteful motions, thereby improving the efficiency and safety of surgeries.
Research Conclusions
Taylor’s research concluded that significant productivity gains could be achieved by standardising work practices and optimising task sequences. He found that systematic planning and worker training could double productivity. Taylor proved that by applying scientific principles to work processes, productivity could increase, and workers could also be spared from unnecessary fatigue and effort. His methods suggested that a well-organized and scientifically managed workplace benefits the employer and the employee. The Gilbreths’ motion studies concluded that reducing unnecessary movements improved efficiency and worker satisfaction. Their work emphasised the importance of ergonomics and human factors in improving workplace efficiency.
Impact and Legacy
The time-motion studies by Taylor and the Gilbreths have profoundly impacted industrial engineering and management. Their methods laid the groundwork for various efficiency and productivity tools used in industries today. Critical implications and transformations include:
- Lean Manufacturing: The principles of eliminating waste and optimising processes are central to lean manufacturing, a methodology widely adopted in industries like automotive and electronics.
- Six Sigma: Six Sigma’s focus on process improvement and defect reduction can be traced back to the precision and standardisation advocated by Taylor and the Gilbreths.
- Human Factors and Ergonomics: The Gilbreths’ emphasis on the human element paved the way for the field of ergonomics, which seeks to design work environments that optimise human well-being and performance.
- Operations Management: The principles of scientific management are integral to operations management, influencing how organisations plan, control, and optimise their production processes.
……………………………………………………………………………………………………………………………………
“Impressions From Time” is a curated series from Leaping Frog about stories from the past that have helped shape modern-day practices in the people and organisation domain.
Leaping Frog, a new-age consulting firm, is an enabler and co-creator in enhancing people and organisational effectiveness. We love doing work in the areas of “Driving Organisational Change and Development”, “HR Systems and Talent Strategy”, and “Leadership and Life Coaching”.
Connect and share, for work and more.
Mail: comm@leapingfrog.in
Website: www.leapingfrog.in
Follow Us: https://lnkd.in/d7TQbsia