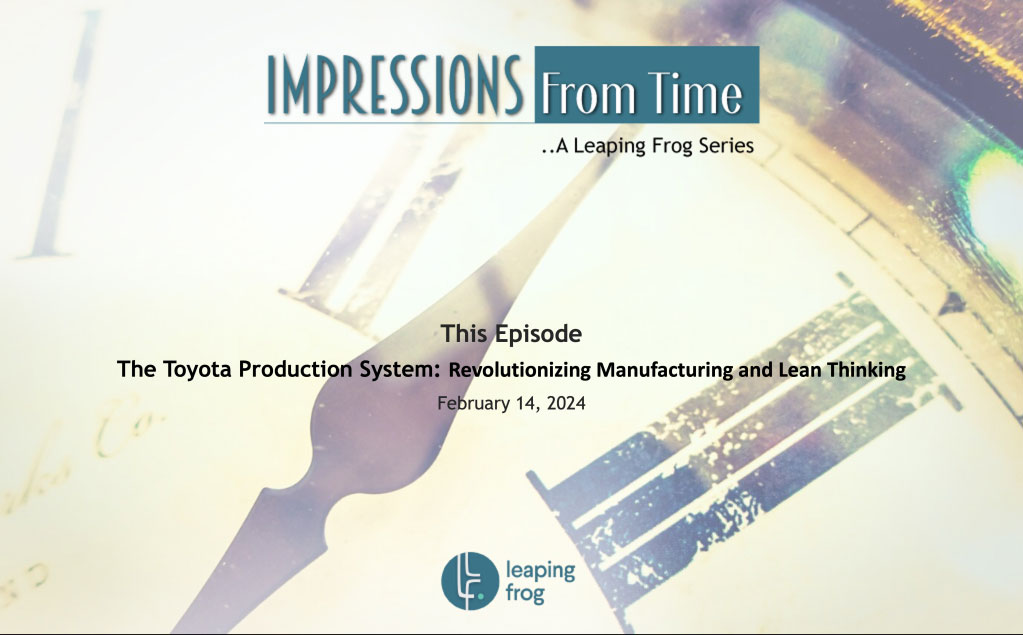
The Toyota Production System (TPS): Revolutionizing Manufacturing and Lean Thinking
The Toyota Production System (TPS): Revolutionizing Manufacturing and Lean Thinking. In the aftermath of World War II, Japan faced unprecedented economic challenges and resource constraints. Among the companies grappling with these harsh realities was Toyota, a burgeoning automobile manufacturer striving to navigate the turbulent post-war landscape. In this adversity, Taiichi Ohno, a visionary engineer at Toyota, embarked on a journey to revolutionise the manufacturing industry and give birth to the Toyota Production System (TPS).
Ohno recognised that traditional manufacturing methods, emphasising mass production and extensive inventories, were ill-suited to Japan’s post-war economic realities. In response, he set out to develop a new approach to production that would optimise efficiency, minimise waste, and empower workers to drive continuous improvement. Thus, the Toyota Production System was born, laying the foundation for a paradigm shift in manufacturing philosophy.
At the heart of TPS were several ground-breaking concepts that would become hallmarks of lean manufacturing. One such concept was “Just-in-Time” production, which aimed to synchronise production with customer demand, thereby eliminating the need for excess inventory and reducing lead times. By producing only what was needed and when it was needed, Toyota achieved significant cost savings and enhanced its responsiveness to market fluctuations.
Another critical pillar of TPS was “Kaizen,” or continuous improvement. Ohno believed that every employee, regardless of their role, had a stake in the improvement process and could contribute valuable insights to drive incremental gains in efficiency and quality. Through a relentless experimentation and problem-solving culture, Toyota empowered its workforce to identify inefficiencies, streamline processes, and drive innovation at every level of the organisation.
The implementation of TPS yielded remarkable results for Toyota. The company experienced significant productivity, quality, and flexibility improvements, setting new standards of excellence in the automotive industry. By leveraging TPS principles, Toyota outperformed its competitors, cementing its reputation as a global leader in manufacturing innovation.
The impact of TPS extended far beyond Toyota’s factories. The principles of lean thinking, embodied in TPS, became a blueprint for excellence in the healthcare and aerospace industries. Organisations worldwide sought to emulate Toyota’s success by adopting lean principles and striving for continuous improvement in their operations.
The story of the Toyota Production System is about the power of innovation and resilience in the face of adversity. By challenging conventional wisdom and embracing a culture of continuous improvement, Toyota transformed the manufacturing landscape and left an indelible mark on the corporate world. The principles of TPS continue to inspire organisations today, serving as a guiding light for those seeking to achieve excellence through lean thinking and relentless pursuit of improvement.
……………………………………………………………………………………………………………………………………
“Impressions From Time” is a curated series from Leaping Frog about stories from the past that have helped shape modern-day practices in the people and organisation domain.
Leaping Frog, a new-age consulting firm, is an enabler and co-creator in enhancing people and organisational effectiveness. We love doing work in the areas of “Driving Organisational Change and Development”, “HR Systems and Talent Strategy”, and “Leadership and Life Coaching”.
Connect and share, for work and more.
Mail: comm@leapingfrog.in
Website: www.leapingfrog.in
Follow Us: https://lnkd.in/d7TQbsia